Membrane Filter Press
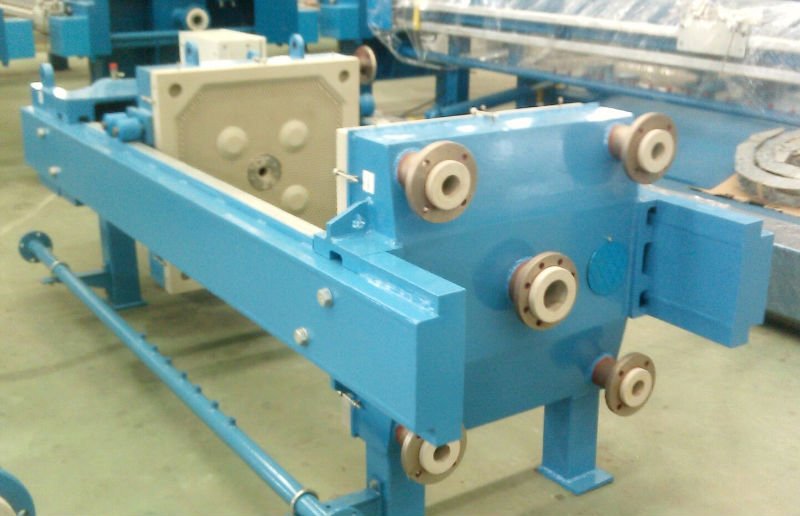
We manufacture membrane filter presses. The membrane squeeze plate is offered to suit up to 16 bar squeezing pressure. Due to additional liquid extraction from the Cake during the squeeze cycle, moisture in the Filter Cake reduces. Filtration cycle time are reduced compared to the conventional recess chamber plate and also Plate and frame filter press, resulting in Benefits of membrane plates v/s chamber plates.
Conventional FILTER PRESSES are limited to using feed pump discharge pressure to produce dry solids, resulting in longer cycle times. The membrane squeeze plate reduces the long cycle time by introducing a squeeze medium of the membrane squeeze plate. This allows the membranes to flex against the cake, compressing and packing it. Filtration cycle are shorter, dry solids are increased, and waste volume is reduced. The membrane is designed to dewater the most difficult Cake and protect the Filter plates against cake less chambers. The high pressure membranes are developed for difficult filtration processes. Extreme squeeze pressures are possible due to the combination of the special feed inlet design and selected special materials.
Conventional FILTER PRESSES are limited to using feed pump discharge pressure to produce dry solids, resulting in longer cycle times. The membrane squeeze plate reduces the long cycle time by introducing a squeeze medium of the membrane squeeze plate. This allows the membranes to flex against the cake, compressing and packing it. Filtration cycle are shorter, dry solids are increased, and waste volume is reduced. The membrane is designed to dewater the most difficult Cake and protect the Filter plates against cake less chambers. The high pressure membranes are developed for difficult filtration processes. Extreme squeeze pressures are possible due to the combination of the special feed inlet design and selected special materials.
pecial Features:
- Shorter cycle time
- Increased dry solids
- Reduced filtration time
- Easily replaceable
- Membrane are common and cab be used on either side of the plate
- Pip style drainage surface design for uniform flex.
- Reduced cake washing time
- Lesser wash water consumption
- Increased capacity
- Lower waste disposal cost
- Lower operating cost
- Excellent cake discharge
- Higher quality and valued end product
- Plate size ranging from 800 x 800 to 2000 X 1500mm
- Membrane: PP/EPM
- Pressure: upto 24 bar
- Controls: Fully Automatic/ Manual
- Hydraulics: upto 650 tons
- Complete Automatic cycle option
Membrane plates are constructed in the same basic method as the recessed chamber plates. The drainage surface of the plates, however are flexible. After filtration, when the chambers are filled with solids and while the filter press is stalled, air / water pressure is exerted behind the flexible drainage of the plate. The membrane in turn inflates or flexes outward and exerts pressure on the filter cake which has been formed. The cakes are then squeezed to reduce the amount of remaining moisture prior to cake discharge.
A Membrane Filter Press, however, can be stopped at the most efficient point in its cycle. By applying pressure to the membrane built into the filter plate, the cake is squeezed to achieve final solids content in a significantly reduced cycle time.
Improved Cake Washing: Our Membrane Filter Presses improve cake washing by initiating a low-pressure pre-squeeze before the wash cycle is begun. This pre-squeeze eliminates channeling (cracks and less well-formed areas of the cake) and produces a uniform, homogeneous filter cake and optimum wash efficiency.
Highest Cake Solids: By applying a high pressure squeeze to the filter cake you can produce the final cake with solids content from 50 to 100% greater than can be achieved with conventional filter presses. This is important for both maximum yield, where a high value liquid is your product, or high solids-content, where reduced moisture in the final cake is critical.
Our Membrane Filter Press provides a dryer cake that can be obtained using high feed pumping pressure in a conventional filter press. It significantly reduces or eliminates downstream thermal drying and associated costs in energy and time.
Corner-Feed for Better Filtration: We recommend corner-feed plates because of their numerous design advantages for virtually every filter press installation. We design these features in our Membrane Filter Presses as well as in our conventional filter presses.
Corner-feed design offers the most efficient cake formation and provides even solids distribution through-out the plate stack. More importantly, eliminating a center-feed eye allows construction of a stronger plate requiring no supporting stay bosses which hamper thorough cake washing and cake discharge.
With a center-feed filter plate, cake washing is difficult due to wash water "short circuiting" through the open center-feed eye. Corner-feed is the only plate design which insures thorough cake washing integrity.
Sizes available:
- 630mm x 630mm
- 800mm x 800mm
- 1000mm x 1000mm
- 1200mm x 1200mm
- 1500mm x 1500mm