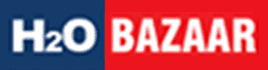
Apr 20
Water treatment means removing all the biological, chemical, or physical substances that can be harmful to the water supply for human consumption and domestic use. This treatment helps produce safe, palatable, clear, colourless, and odourless water. Water also needs to be non-corrosive, which means it should not damage the piping systems.
Urban cities are highly populated, so there is a demand for water supply. As the demand keeps increasing, the need for large volumes of clean and safe water to be supplied is also growing. As the population keeps increasing, the need for continuous supply and finding new sources will also keep rising as the demand grows. Groundwater is a good source as it requires minimal treatment, but surface water like rivers, lakes, wetlands, or reservoirs must be treated to make it safe for consumption and use. So, it’s best to have large water treatment plants for cities to supply water that is drawn from rivers, lakes reservoirs, etc using mechanised means like pumps, compressors, and good pipe systems.
Depending on the volume of water required, the size of the water treatment plant (WTP) can be determined by calculating various factors like types of users, population, the purpose of usage, etc. However, before calculating, we first need to know the different stages in the water treatment process.
A sustainable water treatment process means maintaining it for a long time. Moreover, it has to be simple to operate and maintain. Complex systems should be avoided so that the plant operator, even of a lower cadre can operate easily.
A treatment plant and the distribution system should have a strong build with a long operating life. Hence, the materials used should be strong and durable.
There are mainly six stages in the water treatment process for clean water supply. The utility plant that does the water treatment and distribution must ensure that regular water analysis and quality standards are met for a safe water supply. Let us list the different stages in the water treatment process.
Once the water is collected, it is important to use screens so that any large floating suspended solids like leaves, twigs, paper, rags and other debris that are present can be eliminated before it enters the treatment plant so that it doesn’t obstruct the floe or damage equipment and treatment plants. There are coarse and fine screens.
A Coarse screen can consist of parallel bars, rods or wires, wire mesh or even perforated plates with openings generally of circular or rectangular shapes. These screens obstruct large objects like branches, rags and debris from entering the treatment plant as they also harm the mechanical equipment or clog up the WTP.
The second is the Fine screen that comes after the coarse screens. They are usually perforated plates, wired mesh or micro strainers with smaller openings. These remove fine particles, solids, or algae that float in the water and trap the equipment.
After the screening stage, the water is aerated to remove any odour, soluble gases, undesired taste or organic compounds. Aeration is an important stage in making water safe and pure. It increases dissolved oxygen and reduces carbon dioxide in water.
In this stage, a coagulant chemical is added to the water to neutralise the water and remove suspended solids. Coagulants commonly used are aluminium sulphate, ferric sulphate and alum.
An aluminium compound called alum induces the clumping of suspended particles. The water is now neutralised, and these fine particulates come together forming soft and fluffy particles called flocs.
During the flocculation process, paddles stir the water in a flocculation tank, and the flocs come in contact with each other forming larger flocs. Paddles stir the water in a flocculation tank during the flocculation process, and the flocs come into contact with each other, forming larger flocs.
During sedimentation, large flocs are formed, and they settle to the bottom of the water supply due to their weight. This settling process is called sedimentation. The water is kept in the tank for several hours to allow sedimentation to occur. The floc then settles and accumulates and becomes sludge which is later removed from the bottom of the tank.
When the floc settles to the bottom, the water becomes clear on top and flows through filters of various compositions such as sand, gravel, charcoal, and so on. Backwashing occurs when the filters are full of trapped solids.
After sedimentation, the water is disinfected to eliminate any remaining pathogenic microorganisms. The most commonly used disinfectant is chlorine, in the form of a liquid (such as sodium hypochlorite, NaOCl) or a gas. It is relatively inexpensive and simple to use, and the amount used is less than one milligram per litre. When chlorine is added to water, it reacts with any pollutants present, including microorganisms, over a given period, referred to as the contact time. The amount of chlorine that remains after this is referred to as residual chlorine. It stays in the water all the way through the distribution system, protecting it from any microorganisms that might enter it until the water reaches the consumers.
After the different treatment processes, various wastes arise. During the screening stage, the generated waste is sent to a landfill or disposal site. Fine screening in the form of the slurry may be discharged into a sewer or landfill. The flocs formed from the sedimentation tank is sludge that is either sent to a landfill or a sewage treatment plant.
To know more about the latest water treatment technologies, click H2obazaar.com and get expert advice. Purchase leads exclusively for water treatment products and project information only on h2obazaar.com. You can benefit by consulting with our experts when you have questions about your industrial water treatment process or about which technology might be best for your operations.